Test
and Calibration
|
|
NIST Standard Calibration
Heat Source
|
Liquid
nitrogen
|
Ice
point
|
Liquid
baths
|
Liquid
baths
|
Furnace
|
Furnace
|
Temperature °C
|
-196
|
0
|
5 to
75
|
-25
to 250
|
250
to 500
|
500
to 1100
|
Temperature °F
|
-320.8
|
32
|
41 to
167
|
-13
to 482
|
482
to 932
|
932
to 2012
|
Min. probe length
X
|
12"
|
3"
|
3"
|
6"
|
12"
|
20"
|
|
The manufacturer provides
comparison temperature calibrations from -25 to +250
°C (-13 to 482 °F) using liquid baths and an extended
range using heat furnaces and single point set-ups on
the International Temperature Scale of 1990. Calibrations
are traceable to standards maintained by the National
Institute of Standards and Technology (NIST). Calibration
services are in conformance with ASTM E220, IEC 17025
and ANSI/NCSL Z540-1-1994. The report of calibration
is referenced on the serial number of the temperature assembly.
Three point calibrations
are provided, given that the specified temperatures
are within the recommended range and the minimum length
requirements are met as specified. The minimum length
is based on the overall length "X" of the
spring loaded insert.
-25 to +250 °C can be ordered
using the calibration option in the sensor structure
- extended range must be ordered separately as a service.
|
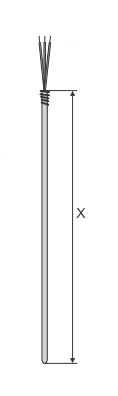
|
Inspection
certificate 10204 - 3.1 The
inspection certificate EN10204 3.1 for medium contact
parts is produced by a department independent of the
production and confirmed by an expert independent of
the production of the manufacturer ("works expert"). The
material tests carried out and the additional quality
control agreed on are certified with detail of the test
results and under supervision of an independent authority.
|
NACE The
NACE MR0175 standard is essentially a listing of materials
that are considered suitable for use in surroundings
containing sulfur hydrogen (sour gas). New suitable
materials are included in this standard after passing
through an extensive approval process (annual update).
|
PMI
(non destructive testing) This non destrucitve
material identification as well as check of welding
connections are frequently used at acceptance tests.
|
Assessment
according to the pressure equipment directives If
the multi-point thermometer is equipped with a safety
chamber, this chamber represents
a pressure containment equipment. This is because in
the case of a fault condition (e.g. thermowell rupture)
this piece of equipment is filled with process pressure.
Depending on the type of fluid, the volume of the chamber
and the process pressure the correspoding conformity
assessment module is consulted and used.
|
X-ray
testing (non destructive test) Faults
like inclusions, pores, tears etc. in the base material
and/or in the welded seam are seen. Furthermore
the exact positioning of the welded components can be
checked.
|
Die
penetration test Red-white-method Suitable
for checking material surfaces and welded seam surfaces.
So for example cracks can be detected. It is applicable
for the welding seams of stainless steels, austentic
materials and metal based alloys.
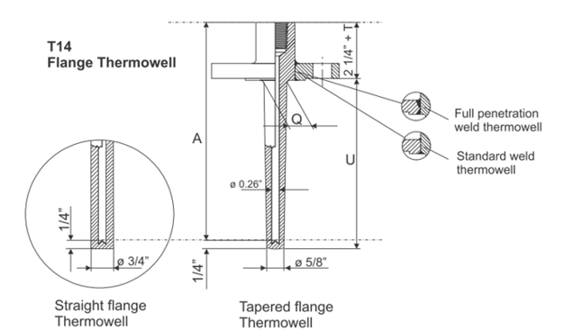
|
Hydrostatic pressure test
internal/external Using
the internal and external pressure test the strength
an pressure tightness of thermowells and process connections
can be checked. For example the internal pressure test
serves for checking the safety chamber connection flanges.
|
Helium leakage test Pressure
tightness test for thermowells, welded seams, screwed
fittings. Depending on the thermometer design and thermometer
size it can be pressurized internally or externally
with helium gas.
|
|
|
|